How Timely Packaging Machine Repair Can Prevent Costly Downtime
How Timely Packaging Machine Repair Can Prevent Costly Downtime
Blog Article
The Ultimate Guide to Packaging Device Repair: Maintain Your Operations Running Efficiently
Understanding the complexities of packaging maker repair is essential for keeping ideal performance and decreasing interruptions. Normal maintenance not just expands the life of these devices however also addresses usual issues that can hinder efficiency.
Significance of Normal Maintenance
Routine maintenance of packaging makers is important for making certain optimum efficiency and durability. By carrying out a structured upkeep routine, drivers can recognize potential concerns before they intensify right into considerable troubles. This proactive technique not just minimizes downtime but additionally expands the lifespan of the devices, ultimately resulting in reduced operational prices.
Regular assessments enable the assessment of important parts such as belts, seals, and sensing units. Addressing wear and tear promptly prevents unforeseen failings that could interrupt manufacturing and result in pricey repairs. Additionally, routine maintenance helps make certain compliance with sector requirements and policies, fostering a safe functioning environment.
Additionally, maintenance tasks such as lubrication, cleaning, and calibration considerably enhance maker effectiveness. Boosted efficiency converts to constant item high quality, which is vital for maintaining client contentment and brand name online reputation. A well-kept packaging maker operates at ideal speeds and decreases material waste, adding to total productivity.
Typical Packaging Device Problems
Product packaging equipments, like any type of complex machinery, can run into a variety of usual concerns that might prevent their performance and performance - packaging machine repair. One widespread issue is inconsistent sealing, which can cause item perishing and wastage if packages are not correctly sealed. This frequently results from misaligned elements or worn securing elements
One more constant problem is mechanical jams, which can occur as a result of international items, used parts, or inappropriate positioning. Jams can trigger hold-ups in production and increase downtime, eventually impacting general performance. In addition, digital malfunctions, such as failing in sensors or control systems, can interrupt operations and lead to unreliable dimensions or erratic maker habits.
Moreover, concerns with item feed can likewise arise, where products might not be delivered to the packaging location regularly, triggering disruptions. Last but not least, wear and tear on rollers and belts can bring about suboptimal efficiency, calling for instant focus to protect against more damages.
Understanding these common issues is important for preserving the stability of product packaging operations, guaranteeing that machinery runs smoothly and effectively, which in turn helps in conference manufacturing targets and maintaining item high quality.
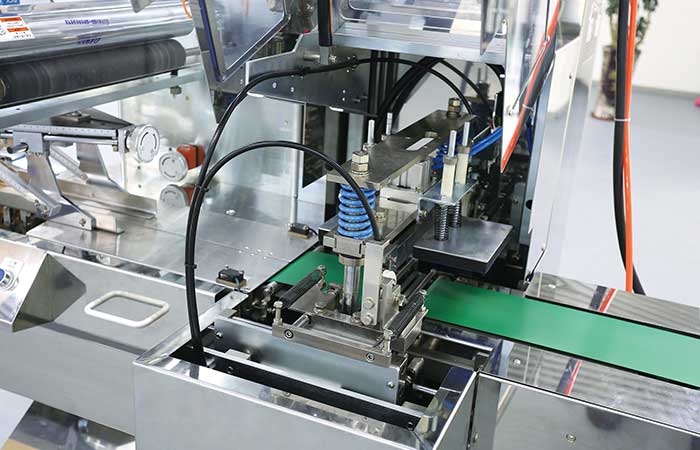
Repairing Techniques
Effective troubleshooting methods are crucial for immediately attending to problems that develop with packaging makers. A methodical technique is important for identifying the origin of breakdowns and lessening downtime. Begin by gathering information about the symptoms observed; this may consist of unusual noises, functional delays, or error codes shown on the machine's interface.
Next, describe the maker's handbook for repairing guidelines details to the model in question. This resource can give important insights into common concerns and recommended diagnostic actions. Use visual assessments to check for loose links, worn belts, or misaligned elements, as these physical elements usually add to operational failings.
Execute a process of removal by testing individual device functions. If a seal is not creating correctly, assess the securing device and temperature level settings to determine if they satisfy functional requirements. File each step taken and the results observed, as this can assist in future fixing efforts.
Repair service vs. Replacement Choices
When confronted with equipment breakdowns, determining whether to repair or change a packaging device can be a complicated and essential choice. This decision depends upon a number of vital factors, including the age of the machine, the degree of the damage, and the predicted effect on operational performance.
First of all, take into consideration the device's age. Older equipments might need even more frequent fixings, bring about higher collective expenses that can exceed the financial investment in a new unit. Additionally, review the seriousness of the malfunction. Minor problems can typically be fixed rapidly and affordably, whereas extensive damage may demand a considerable financial commitment for fixings.
Functional downtime is another vital discover here consideration. Spending in a new device that offers boosted performance and dependability could be more prudent if repairing the device will cause prolonged hold-ups. Think about the accessibility of parts; if substitute elements are tough to come by, it may be more strategic to replace the machine completely.
Eventually, carrying out a cost-benefit analysis that includes both instant and lasting implications will assist in making an informed decision that straightens with your financial restraints and functional goals. (packaging machine repair)
Preventative Actions for Long Life
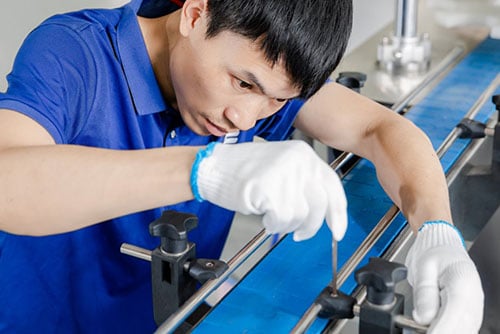
Secret preventive steps consist of regular lubrication of relocating components, alignment checks, and calibration of controls and sensors. Establishing a cleaning routine to remove debris and impurities from equipment can significantly minimize wear and tear (packaging machine repair). In addition, monitoring functional specifications such as temperature and vibration can help find abnormalities early
Educating staff to acknowledge signs of wear or breakdown is another critical component of preventative upkeep. Encouraging operators with the understanding to perform fundamental troubleshooting can result in quicker resolutions and lessen functional interruptions.
Paperwork of upkeep activities, including service records and inspection searchings for, promotes responsibility and helps with informed decision-making relating to repairs and substitutes. By focusing on preventative actions, organizations can ensure their product packaging equipments operate at peak efficiency, ultimately leading to boosted productivity and decreased functional expenses.
Final Thought
In conclusion, the reliable upkeep and repair service of product packaging machines are extremely important for sustaining operational efficiency. By executing preventive actions, businesses can enhance equipment long life and ensure nonstop efficiency in product packaging procedures.
Understanding the intricacies of product packaging equipment Learn More Here repair work is essential for preserving optimum performance and minimizing disruptions.Regular upkeep of product packaging makers is critical for ensuring optimal efficiency and longevity.Packaging equipments, like any kind of complex equipment, can come across a selection of typical issues that may hinder their efficiency and effectiveness. If repairing the maker will certainly create prolonged hold-ups, spending in a new device that Discover More provides boosted performance and dependability may be extra prudent.In final thought, the reliable maintenance and repair of packaging machines are paramount for maintaining operational efficiency.
Report this page